- Notus
See the invisible, improve the unseen
The future of wind turbine blade inspection is here
- Flawless protection, zero damage
Ensuring durability with non-destructive coating inspection
- Total quality control
Comprehensive inspection of all coating layers. - No contact, no damage
100% non-destructive and non-ionizing technology. - Unmatched precision
Ā Excellent repeatability (<2.5%) and reproducibility (<5%).
- Adaptable to any environment
Works in the lab, factory, or field. - Compatible with all substrates
Composites (carbon or glass) and metals (steel, aluminum, titanium, magnesium, etc.).
Solving a major challenge in the wind industry
30%
Over 30% of blade maintenance costs come from surface defects
1 in 3
1 in 3 repairs must be redone due to inaccurate inspections
⬠2.000
The maintenance costs for wind turbine blades can reach ā¬2,000 for each megawatt of energy the turbine can produce.
Traditional inspection methods fall short
Visual inspections lack reliability
Visual inspections are the most commonly used method for assessing blade coatings, but they rely heavily on the inspectorās experience and subjective judgment. This means defects can be easily overlooked, especially when they are beneath the surface. Furthermore, environmental conditions such as lighting or weather can impact visibility, leading to inconsistent results.
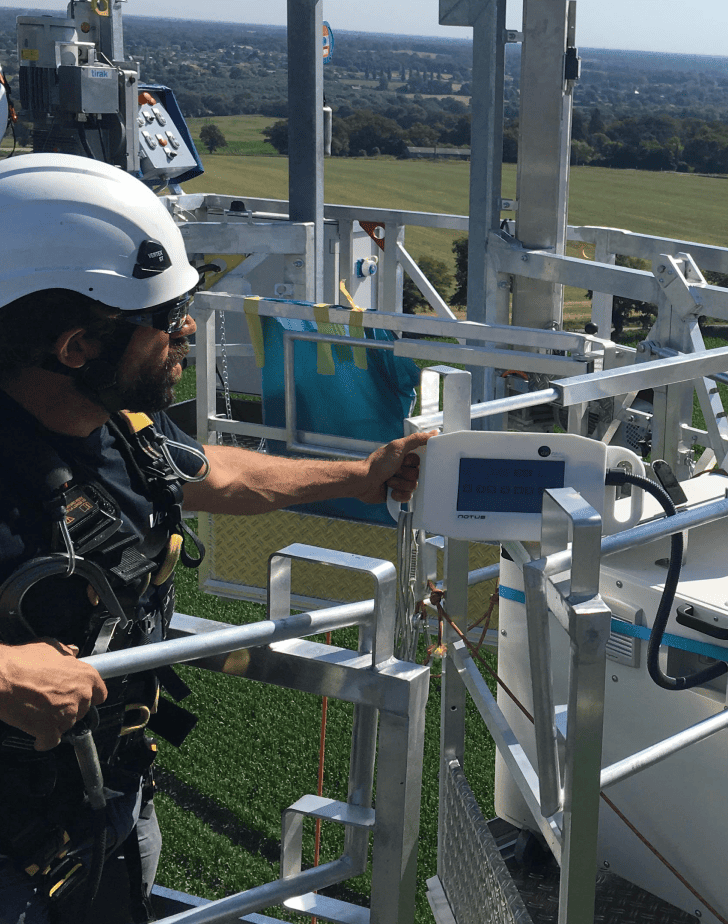
Ultrasound and eddy currents measure only a single layer
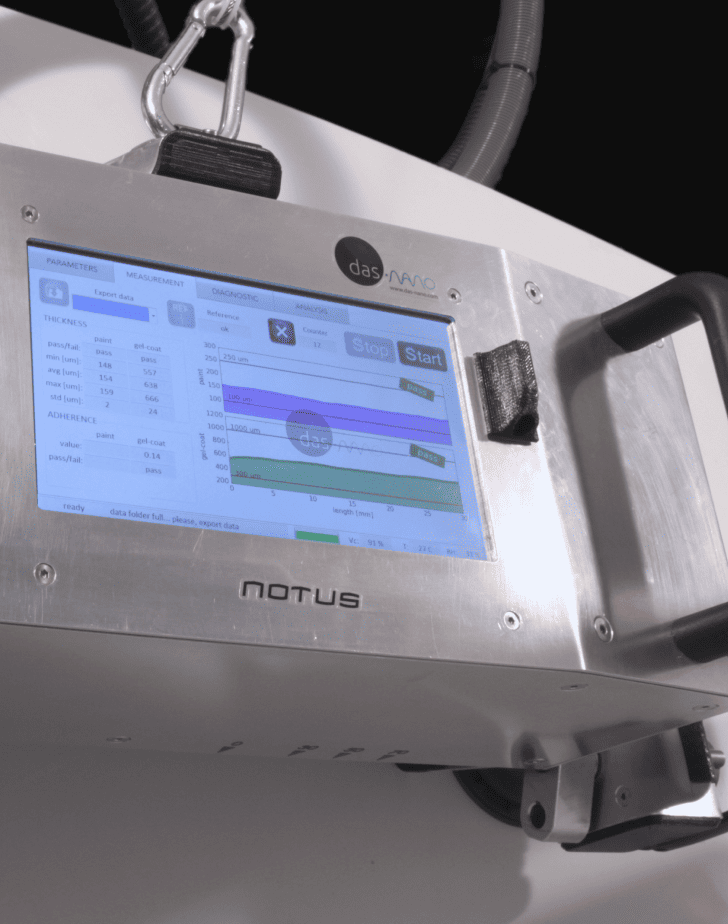
Require highly trained personnel
With Notus, you get full control
- Precise measurement of each coating layer thickness
- Evaluation of paint adhesion to the blade surface
- Detection of invisible defects like bubbles, pores, and orange peel
- Identification of voids and gaps in structural adhesive joints
Watch Notus in action!
Running 24/7 since its installation, it provides unprecedented data on the painting process, enabling a 15% cost reduction through material, energy, and defect minimizationādelivering both economic and environmental benefits.
Three versions tailored to your needs
Notus-Lab | Automated Desktop System
Designed for R&D and material testing, Notus-Lab delivers high-precision, high-speed coating analysis for wind energy and aerospace laboratories. With an automatic measurement process and no sample preparation required, it ensures accurate material characterization across all substrates.
Notus-Factory | Automated Robot-Mounted System
Aimed at wind blade manufacturers, Notus-Factory integrates seamlessly into production lines, inspecting large surfaces with high-speed, high-accuracy measurements. Laser triangulation ensures optimal positioning, reducing material waste and rework costs.
Notus-Field | Manual Vacuum-Assisted System
Developed for wind farm operators and maintenance teams, Notus-Field allows on-site blade inspections with unmatched accuracy. Its vacuum-assisted grip ensures secure placementāeven on vertical surfacesāwhile delivering fast, easy-to-interpret results in seconds.
- Full Blade Inspection:Ā 1 hour | 25 sections | Over 3,000 data points
- Multi-layer thickness & adhesion assessment
- Contact
Ready to transform your inspections?
With Notus, preventive maintenance becomes a realityāreducing costs, improving efficiency, and ensuring wind turbine blades last longer.