- Automotive
The paint shopās gateway to saving time, materials & energy
das-Nano’s Irys system automates previously manual tasks in automotive paint shops, transforming quality control in ways that increase efficiency and sustainability. The installation of Irys leads to significant cost savings in materials and time, driving more efficient and eco-friendly manufacturing practices.
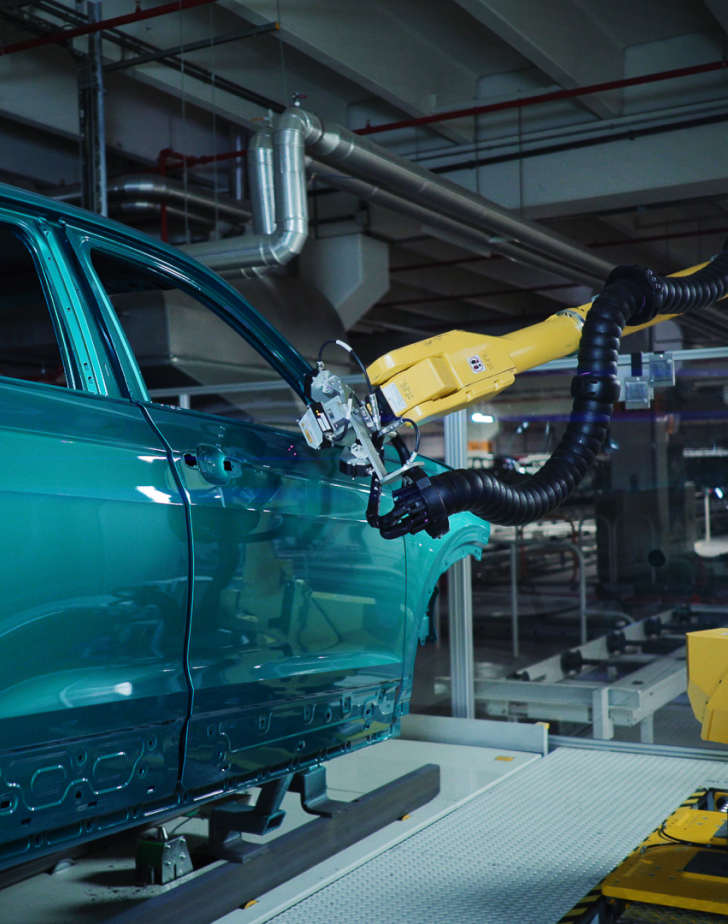
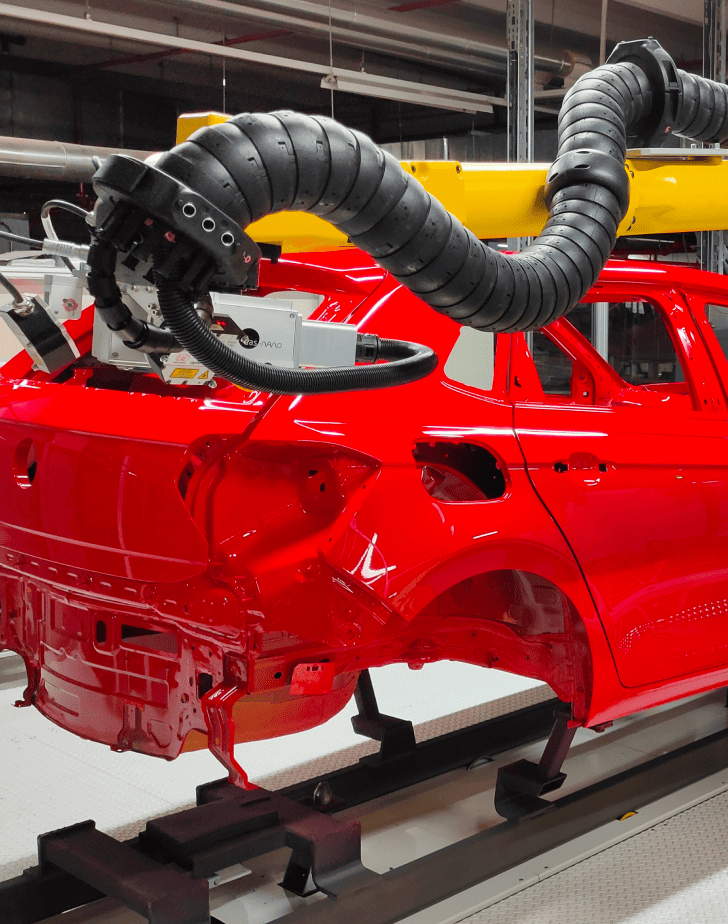
- Boosting efficiency
5%
Less material
15%
Total savings
3%
Fewer reworks
Real-time, non-destructive thickness measurements allow manufacturers to detect and correct deviations before they become costly defects. This proactive approach reduces the need for reworks and ensures a more consistent, high-quality finish.
Gain full control over coating processes for a more sustainable, cost-effective, and reliable paint shop
ROI in <1.5 years
Unmatched execution speed
- Driving quality and innovation forward
Leading automotive manufacturers trust our technology
The worldās leading automotive manufacturers have extensively tested our terahertz-based technology and reached the same conclusion: it outperforms traditional methods and has the potential to become the new industry standard. As they move away from outdated measurement techniques, they are rapidly adopting our solution to gain a competitive edge, improve manufacturing efficiency, and ensure the highest quality standards in their paint processes.
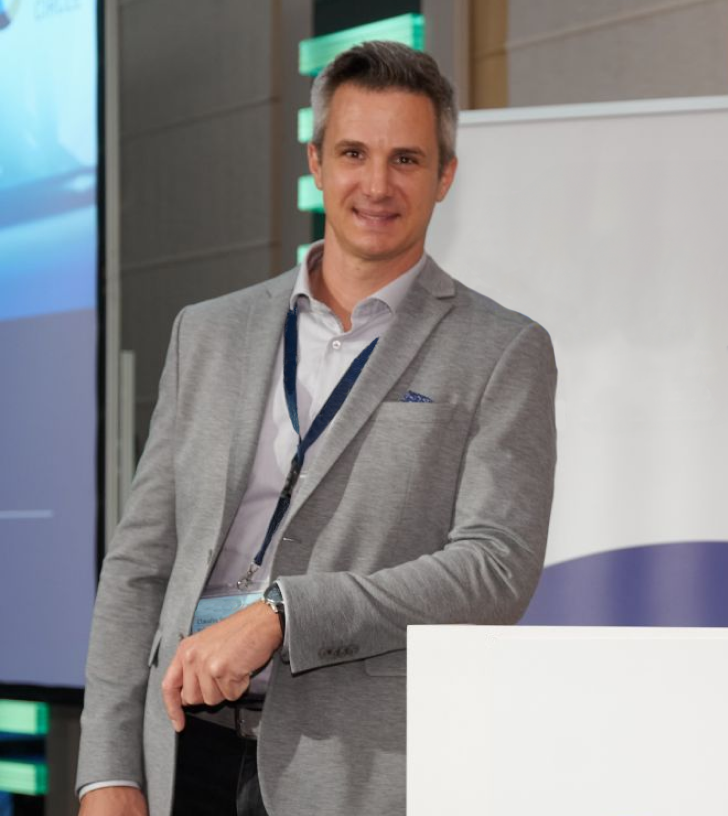
“With previous methods, we needed manual processes to measure layer thickness.
Now, with das-Nanoās terahertz technology, we have significant time and material savings.”
Claudio Sole
Paint Expert, Volkswagen HQ
- Highlights from our blog
das-Nano at the forefront of industrial transformation
- A game changer in car body painting control
Advanced solutions to overcome car body painting control challenges
A new technology standard that eliminates costly and partial manual measurement processes
With Irys, das-Nano automates the coating thickness measurement process, eliminating manual, costly, and inaccurate procedures. Our technology provides precise, reliable measurements in real-time, enhancing productivity and reducing costs.
Accurate, layer-by-layer thickness measurement for complete coating control
Irys offers the ability to measure the thickness of each individual layer of the coating, ensuring full control over the entire paint process. This allows for more accurate quality control and optimization, ensuring that each layer is applied correctly.
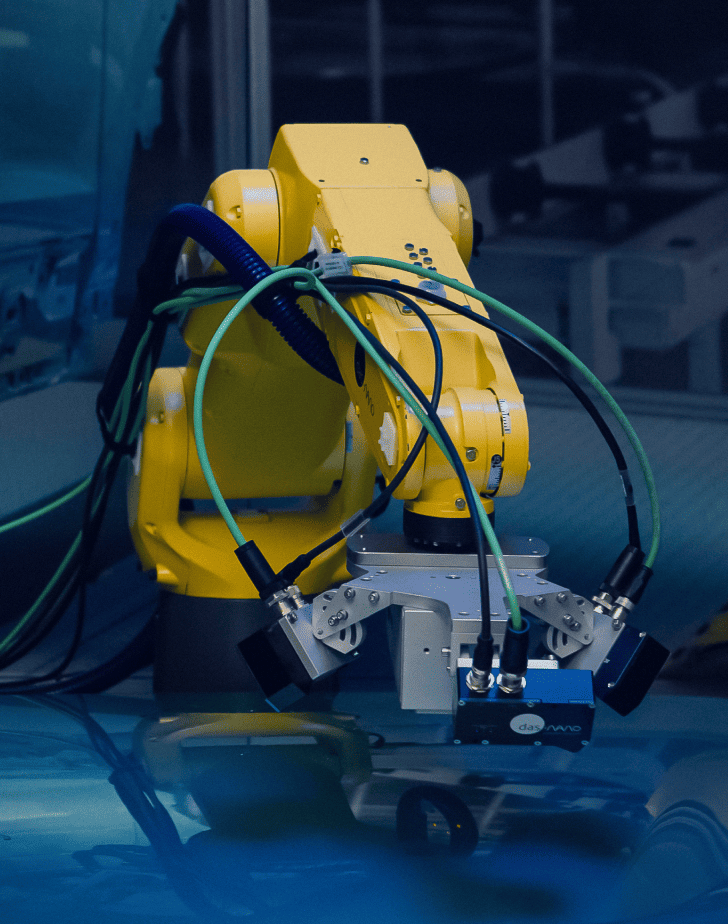
Versatile technology that works on both metallic and plastic components
Unlike traditional systems limited to metallic surfaces, Irys works seamlessly on a variety of materials, including plastic components like rearview mirrors and bumpers, offering a universal solution for all car parts.
Non-contact technology that protects paint and varnish from damage
Irys uses terahertz-based, non-contact technology, ensuring no physical interaction with the car body. This minimizes the risk of damage to the paint and varnish, maintaining the quality and finish of the vehicle’s surface.
Advanced systems that measure coatings on curved and complex surfaces
Irys is not restricted to flat surfaces. Our system is designed to measure coatings on complex, curved surfaces, ensuring full coverage and precision in any manufacturing setup, regardless of the geometry of the car body.
- Compare
Because not all technologies are created equal
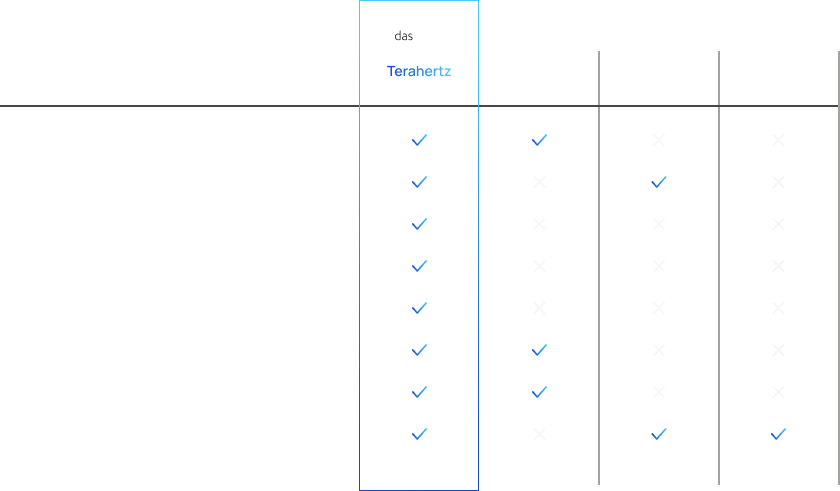
- Say goodbye to coating pain points
Outdated methods are holding you back ā it's time to embrace the new standard in coating thickness measurement
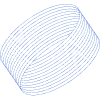
Lack of accuracy
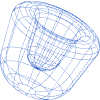
Costly and partial manual processes
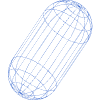
Thickness measurements of the entire coating, not each layer
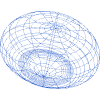
Contact systems with potential damage
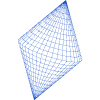
Technology limitations on substrates
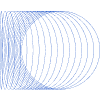
Systems valid Only for flat surfaces
Minimizing Environmental Impact
The automotive sector is increasingly focused on reducing its environmental footprint. das-Nanoās technology not only improves efficiency but also significantly reduces energy consumption and CO2 emissions in the painting process.
50 kWh
7,000 tons annually
- Success Stories