- Batteries
Terahertz technology for battery manufacturing quality control
Leading the way in battery quality assurance with precision and speed
As the demand for electric batteries increases across various sectors, driven by the growing need for energy storage in everything from electric vehicles (EVs) to consumer electronics, the battery manufacturing process faces increasing pressure to meet higher standards of performance and efficiency.
With the rapid expansion of production lines, ensuring consistent, high-quality production is criticalāyet traditional measurement techniques often fall short. That’s where das-Nano’s terahertz technology steps in.
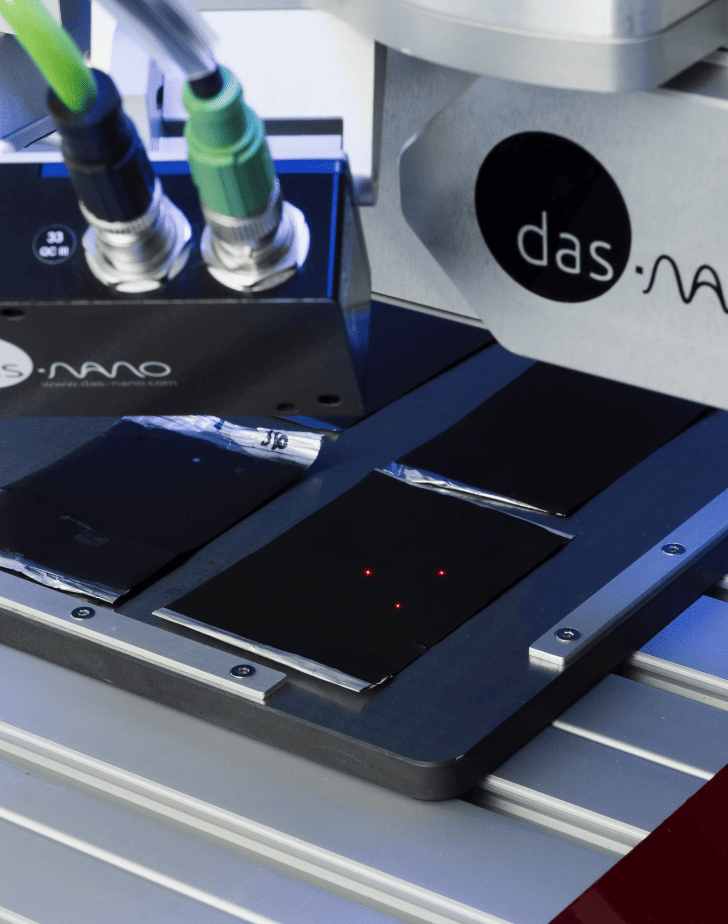
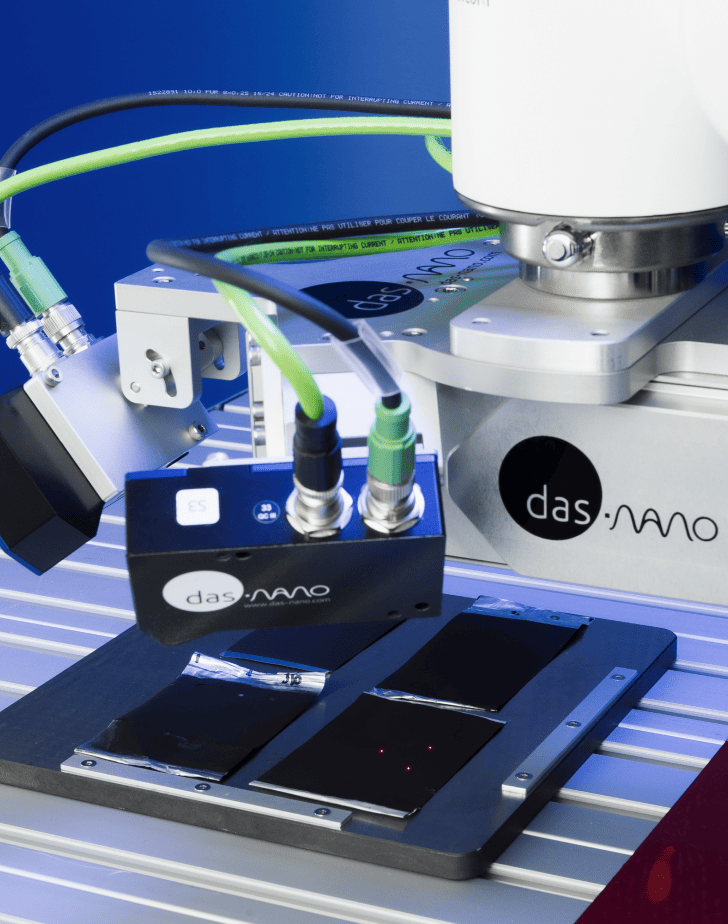
Electrode quality: A key factor for high-performance batteries
In battery manufacturing, the electrode is the most expensive component, representing up to 50% of the total cost. Its quality is crucial for the energy density, lifespan, and safety of the battery. Precision in layer thickness and homogeneity is essential for optimal performance.
However, traditional methods, such as beta and X-ray radiation, fail to provide consistent, reliable results. They measure total thickness (foil + coating), leading to measurement errors that accumulate over time, affecting production quality and efficiency.
das-Nano’s terahertz measurement technology provides a non-contact, non-destructive, and real-time solution that directly measures the coating thickness. This technology measures in less than 5 milliseconds, offering exceptional speed and precision, which is crucial in the fast-paced world of battery manufacturing.
Unlike traditional techniques, terahertz waves measure the coating’s thickness directly without requiring differential measurements. The result? Reduced errors, fewer discrepancies, and a more consistent product.
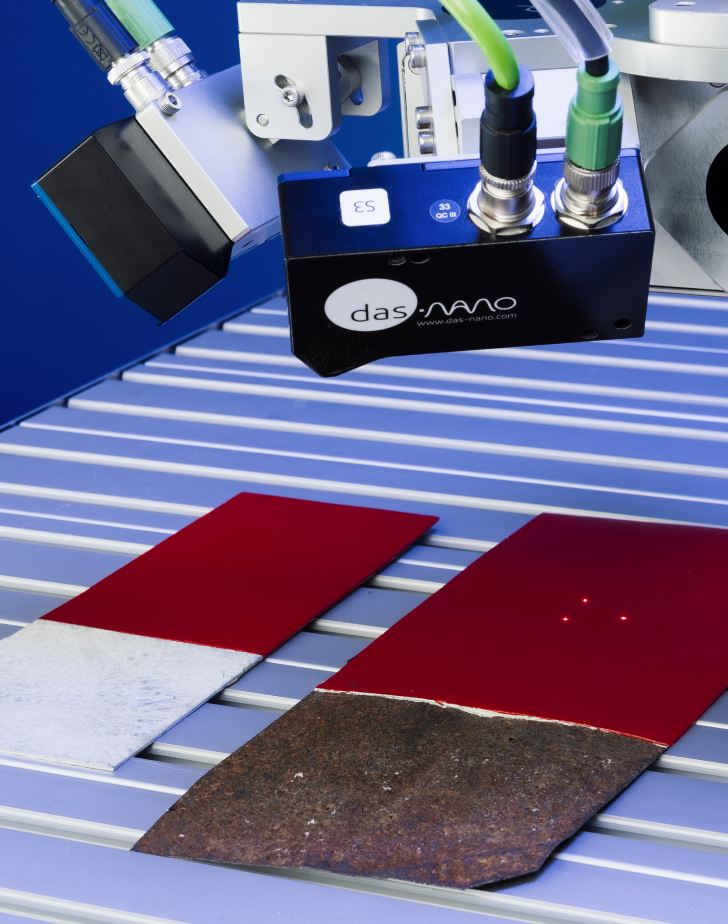
- Efficient optimization
Key benefits of terahertz technology in battery production
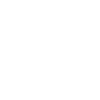
Faster, more accurate measurements
Over 1,000 measurements per second provide real-time data, ensuring consistency throughout production.
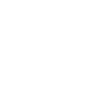
Material savings
By reducing defects and eliminating waste, our technology minimizes material loss and avoids costly reworks.
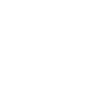
Environmental impact
The efficiency of terahertz technology helps reduce the carbon footprint by optimizing resource usage and speeding up processes like coating and drying.
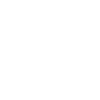
Cost-effectiveness
With real-time measurements and fewer defects, battery manufacturers can lower operational costs and increase ROI.
The ability to accurately measure layer thickness, porosity, and electrode adherence is vital for ensuring battery longevity and safety. With terahertz measurement technology, manufacturers can confidently:
- Improve the batteryās energy density by ensuring homogeneous electrode coatings.
- Reduce internal resistance, enhancing performance.
- Prevent safety issues by detecting inconsistencies early, avoiding overheating or other potential hazards.
As a result, the entire process becomes more efficient, with significantly reduced waste, improved quality, and lower costsāan essential combination in todayās competitive market.
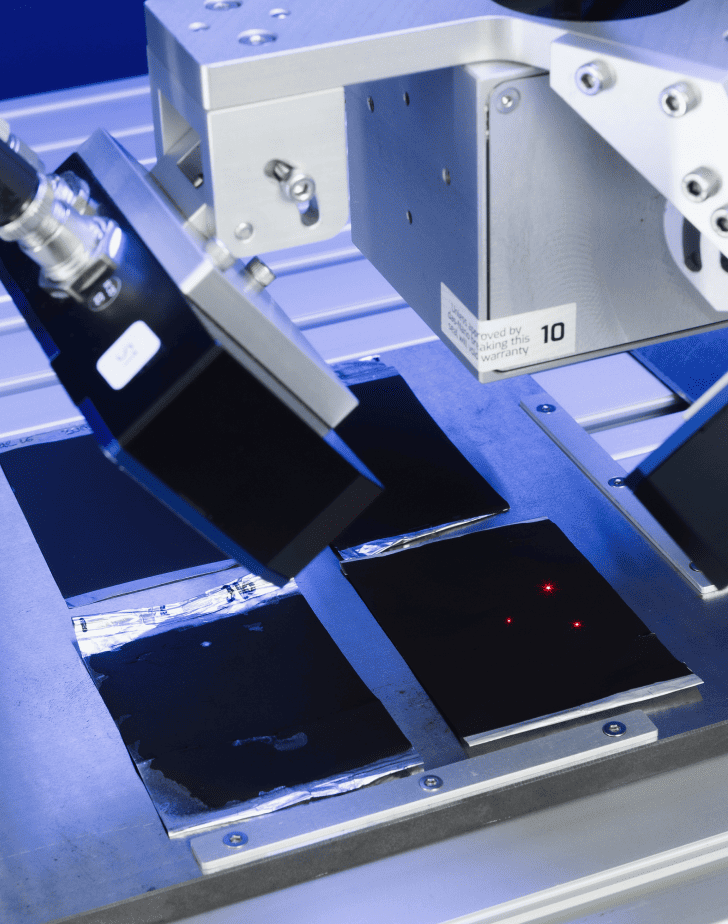
- WHITEPAPER
All you need to know about coating thickness technologies in automotive
A comprehensive guide on coating thickness measurement technologies, their applications, and how they impact efficiency, cost, and sustainability in automotive manufacturing.