- ABB
das-Nano and ABB provides unprecedented savings of time and quality improvements in industrial painting processes
ABB is a leading global technology company that energizes the transformation of society and industry to achieve a more productive, sustainable future. By connecting software to its electrification, robotics, automation and motion portfolio, ABB pushes the boundaries of technology to drive performance to new levels.
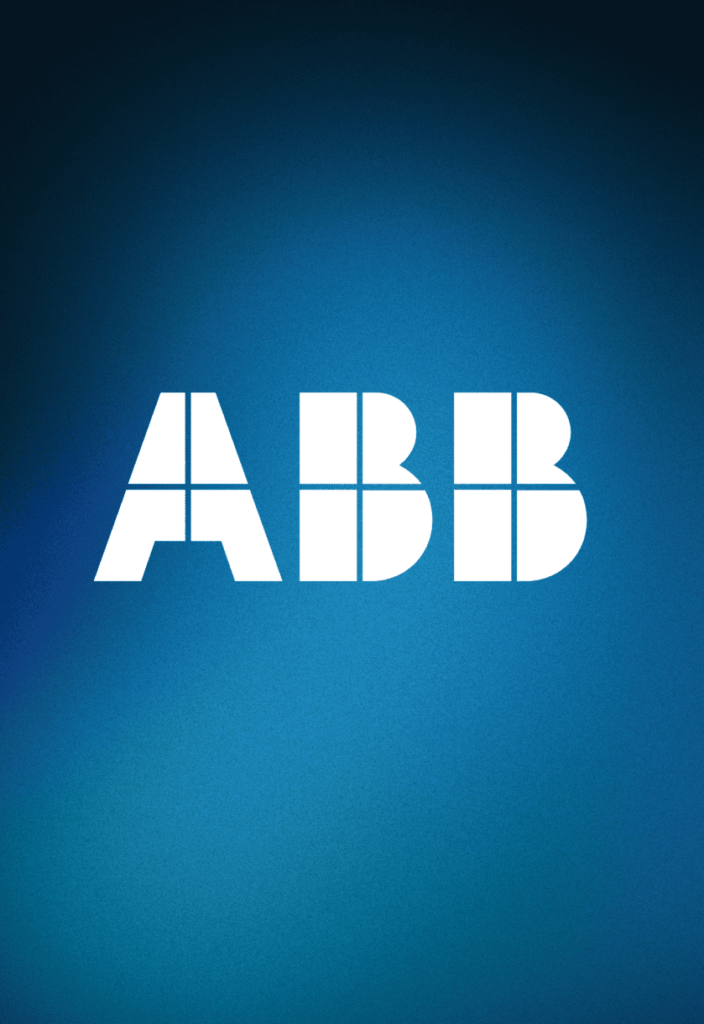
Solution
das-Nano Irys & GoFa⢠from ABB
Coating thicknesses are critical information in the surface treatment industry to ensure the quality and durability of the final product. Insufficient or inadequate thickness can lead to technical problems or high costs.
- das-Nano Irys, a terahertz waves technology, provides a contactless measurement of each layerās thickness in multilayer coatings
- ABB’s latest generation GoFa⢠cobot allows increasing the capabilities of an application by giving more flexibility to the processes. Easy to use and program, it offers high accuracy, safety, and quality.
- The combination of both technologies, collaborative robotics and terahertz wave system, allows laboratories to achieve the best quality and accuracy in measuring the thickness of each layer in the coatings.
Inadequate lab systems to measure the coating thickness
One of the most common problems that laboratories have when characterizing coatings is that they do not have adequate systems to measure the thickness of the coating layers, because these systems are technically insufficient or they are different from those used in the manufacturing line.
Comparable online and offline (in the laboratory) measurements are necessary.
However, most of the current technologies used in manufacturing lines are manual or require contact, and therefore, are slow processes. Other systems do not allow measuring each layer thickness, but measure the total thickness of the coating instead.
Contactless, automatic and fast measurements of each coating layer of wet, dry and cured materials are a must for a R&D or quality control laboratory, to characterize test samples and correlate the thickness results with the production line results.
- Eco Innovation
das-Nano Irys with an ABB collaborative robot is the solution!
Traditional manual methods that require contact and measure the total thickness of the entire coating, not of each layer and spots of the coating: LESS ACCURACY
das-Nano Irys & ABB: fully automated, fast, accurate and contactless system that measures each coating layer simultaneously
- Measurement: less than 5 seconds per point (including robot movements).
- With a system with two heads, you can measure more than 3000 points in a day.
- With 50 points per vehicle, you can inspect more than 600 vehicles per day.
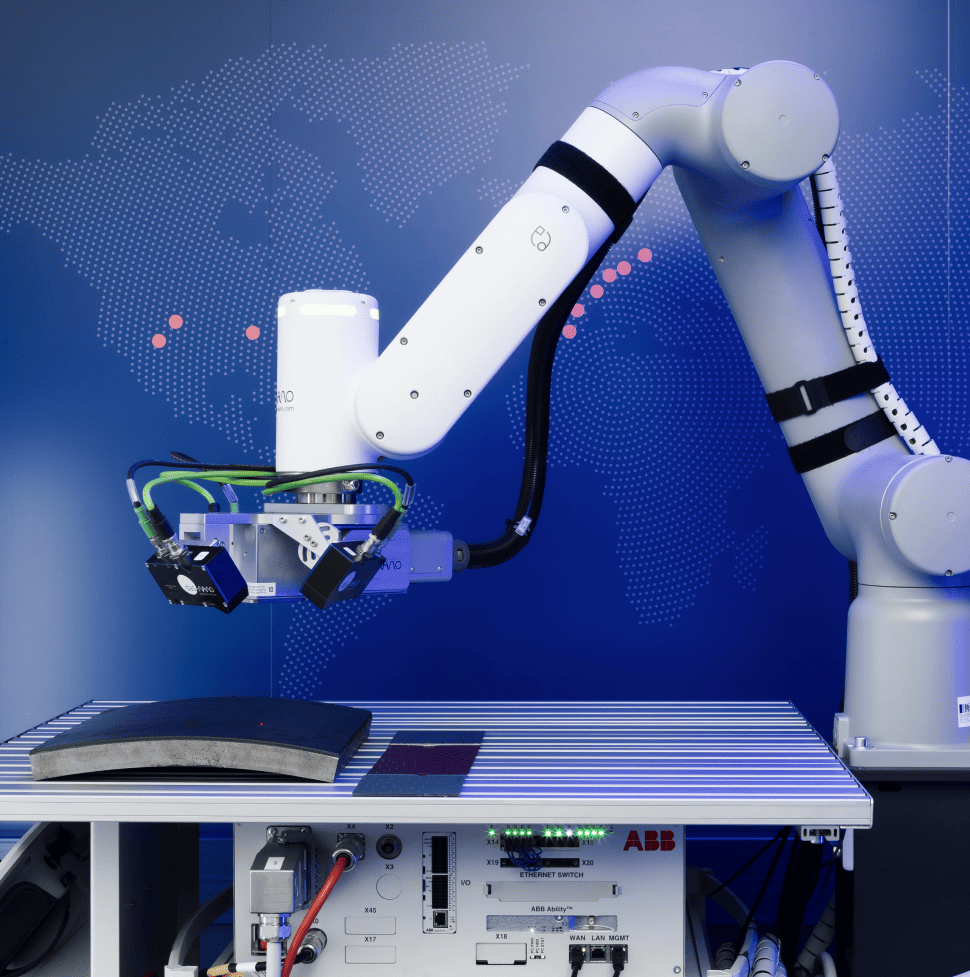
das-Nano Irys with ABB collaborative robot
Our patented technology has major advantages over other solutions on the market. It is a fully automated, fast and accurate system that measures each coating layer simultaneously, regardless of the substrate material. In addition, there is no need for calibration stops during measurement, which saves a lot of time ā And all this without contact!
Work has been carried out in different areas and, in particular, in developing complex algorithms based on artificial intelligence to extract thickness values from terahertz waves and optimize the hardware of the terahertz system to adapt technology to specific measurement needs.
das-Nano Irys system can be adapted to industrial robots to be exploited in production lines and adapted to ABB collaborative robots used in labs. The thickness results in both environments are obtained with the same terahertz technology and are therefore directly comparable.
5% Material Savings thanks to thickness optimization.
Reduction of the environmental impact.
3% Reduction of reworks.
No need for cost extensive calibrations.
Irys features
1. Cost Savings: Time, Materials & Energy
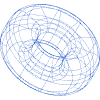
2. Reduction in Reworks & Wastes
Minimizing errors and waste in the production process is a central objective for sustainable and economically sound operations. Manufacturers aspire to implement precision technologies that reduce the need for reworks and minimize material wastage.
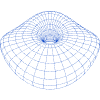