- Siemens-Gamesa
Siemens-Gamesa, prevention of turbine“s casing internal damage
Siemens-Gamesaās years of experience as a pioneer in the wind industry have enabled them to offer cutting-edge technology that harnesses the power of wind and unlocks its future potential to address todayās greatest challenge: the climate crisis:
- Industry: wind energy
Headquarters: Zamudio (Spain), Munich (Germany) - Production: more than 35 years of experience and more than 90 GW installed worldwide
- Employees: 23,000 employees worldwide
- Industry: wind energy
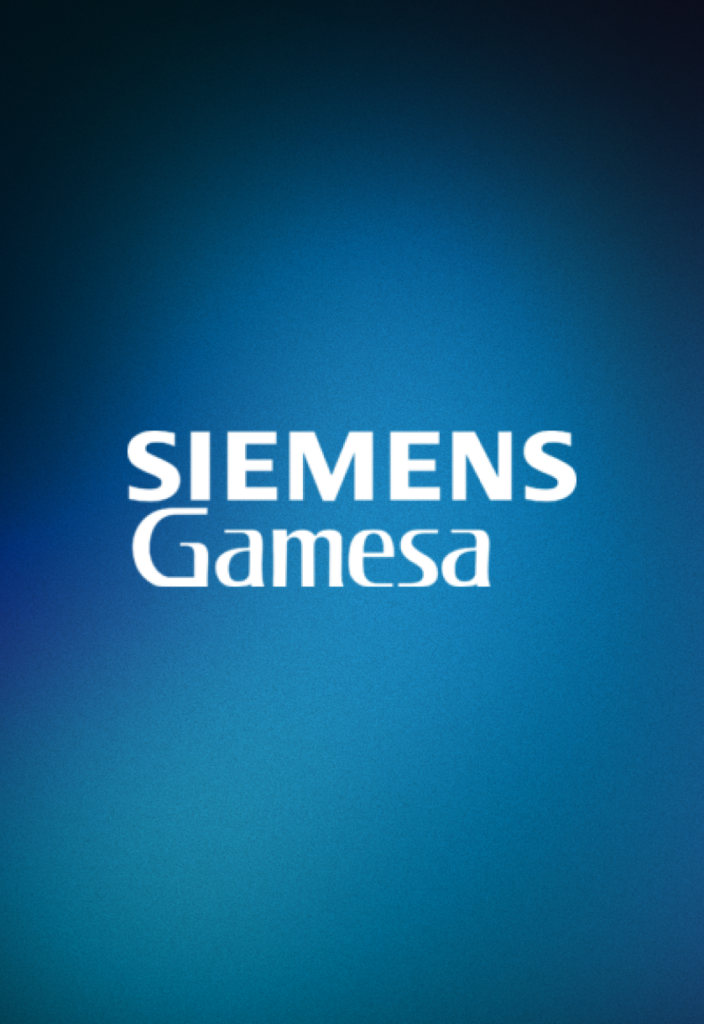
The Siemens-Gamesa challenge How to reduce production downtime due to damaged blade coatings
The wind energy sector faces significant economic losses due to turbine failures, leading to long downtime and costly O&M (operations and maintenance) activities. Such failure is often due to blade coating damage, which cannot be detected by industry-standard quality control processes.
The blades are the most critical component of the turbines due to their structure, size, and exposure to environmental conditions. Therefore, blades are always protected with optimized coatings, consisting of several layers of advanced materials, which must meet high-quality requirements to ensure the smooth operation of the turbines. Thirty percent of O&M costs in the wind industry are focused on the inspection or repair of blade coatings. To reduce these costs, it is crucial to ensure the quality of any blade before installation, to avoid premature failures; and to detect coating defects on operating blades, to prevent undesirable shutdowns.
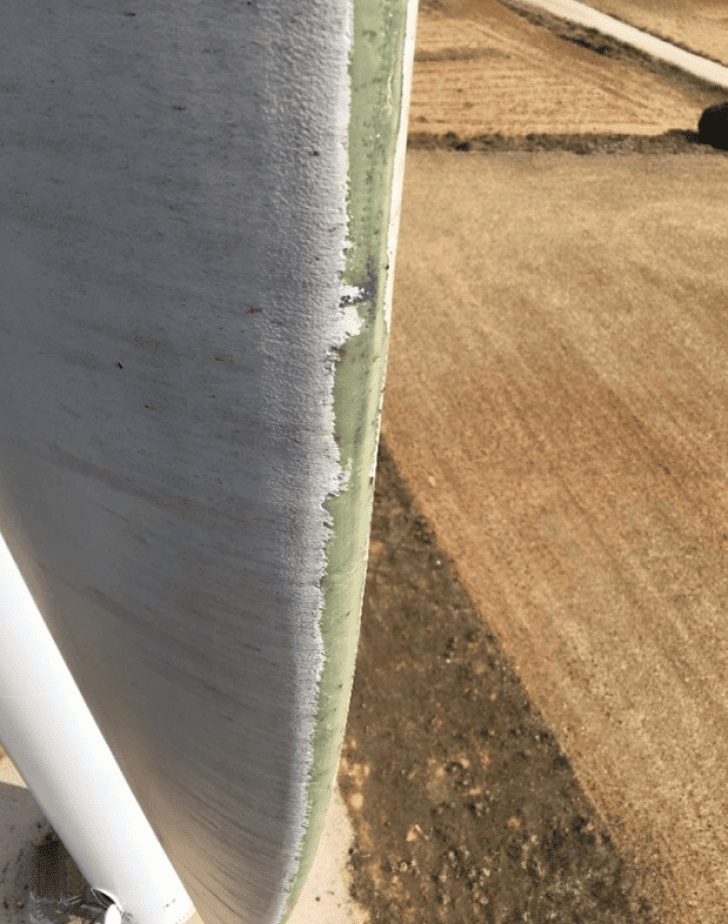
Traditionally, quality control of blade coatings has been carried out solely by visual inspection. However, due to exposure to high thermal, mechanical, and chemical stresses, the internal integrity of the coating often fails, being unnoticeable to the eye. In addition, small external defects often hide much larger problems on the inside, and repair based on visual inspection cannot solve the problem. Currently, at least 1/3 of repaired turbine parts end up needing repair operations in the future. For quality control of internal layers, sometimes only destructive statistical analysis is used, without solving the related cost issues.
Many efforts are being made to develop new non-destructive technologies for material inspection, and das-Nano has come up with the solution after years of research.
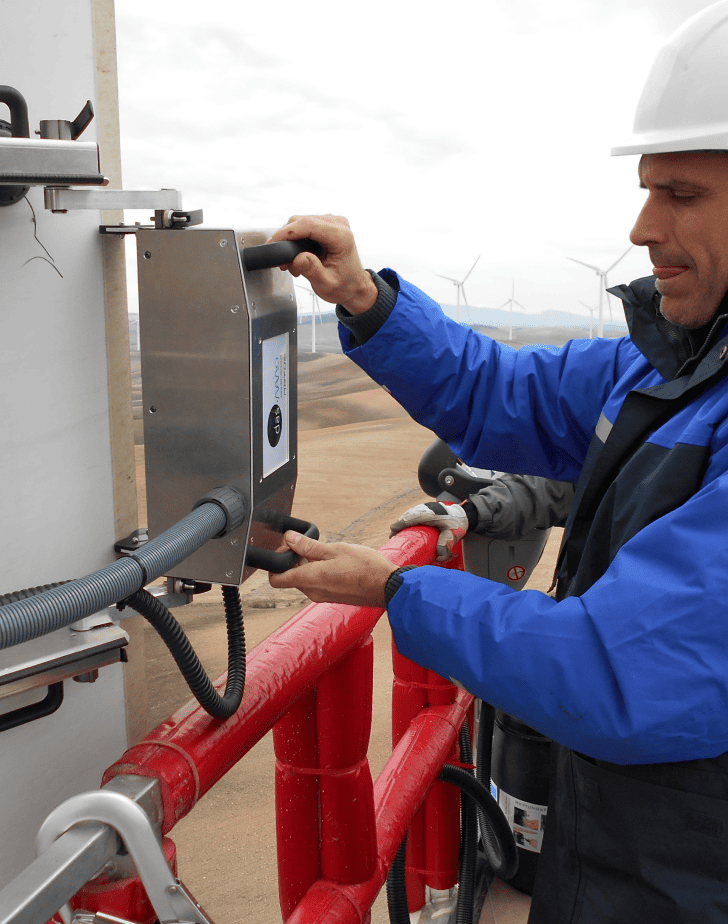
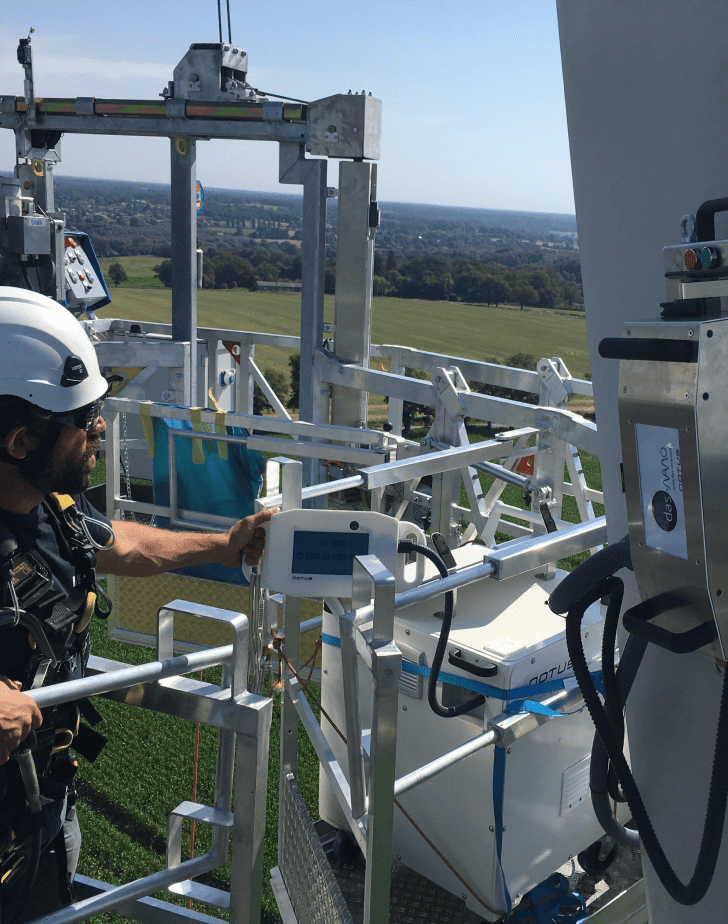
- The das-nano solution
A patented technology for nondestructive detection of internal blade damage
das-Nano, aware of this problem, has developed NOTUS, the only non-destructive inspection tool on the market capable of effectively detecting internal damage in blade coatings. NOTUS, based on terahertz technology, allows the inspection of the thickness measurement of each complete layer and the control of the adhesion of each coating layer on the composite materials used in the wind industry. It works with any substrate: composite (carbon or glass) and metallic (steel, aluminum, titanium, magnesium, etc.). With the possibility to operate in the lab, factory or in the field. NOTUS is seeing what was invisible until now.
NOTUS implementation shows a potential annual economic saving of 10% of O&M costs for wind farm operators, which represents a great opportunity, considering that today there is an annual O&M expenditure in the wind energy industry of 15 billion.
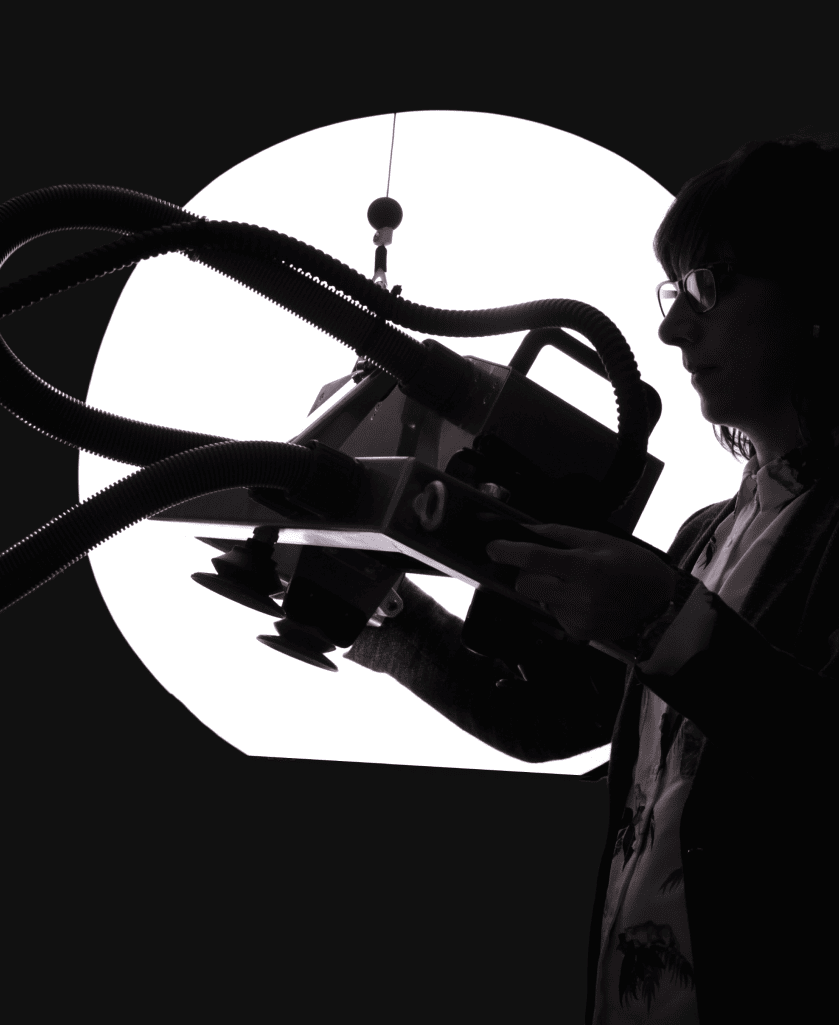
The results: a more reliable and lower cost blade coating control
A more reliable and lower cost blade coating control is achieved by implementing terahertz waves in the quality control of the blades manufacturing. Thanks to the particular properties of this specific frequency of the electromagnetic spectrum, this state-of-the-art non-destructive inspection method is now commercially available.
Siemens-Gamesa has relied on the NOTUS system since 2017 for the blade coating manufacturing quality control. Thanks to this technology, Siemens-Gamesa can have real-time data on the condition of its blade coatings, both during production and throughout their useful life. NOTUS is a portable device that can be used not only in the manufacturing plant, but it can also be taken to logistic hubs and wind farms to perform measurements for preventive or corrective maintenance.