- Volkswagen
Volkswagen, the world´s first terahertz car body paint inspection system
The Volkswagen Group, the world’s largest automobile manufacturer, has decided to use das-Nano technology to measure the layer thickness of its car body coatings.
- Industry: Automotive
- Country: Germany
- Production: 117 production sites in 20 European countries and 10 other countries in the Americas, Asia, and Africa.
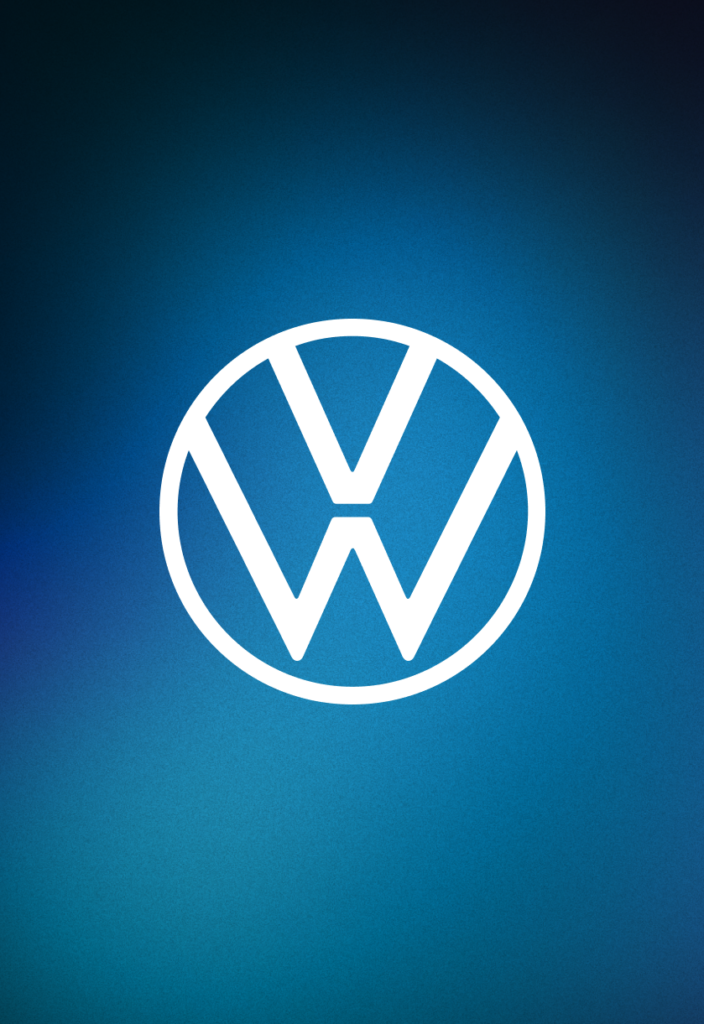
The Volkswagen challenge How to improve the control of the car body painting thickness
The competitiveness in the automotive sector is very high and therefore it requires the most exigent in-line quality control processes. However, the current worldwide used quality control methods for the car body coating thickness measurement presents several flaws that had to be addressed with a new technology:
- They require contact that can damage the car body paint and varnish.
- They measure the thickness of the entire coating, not of each layer.
- They are only valid on metallic substrates, but not on plastic components, such as rearview mirrors and bumpers.
- Some of them are manual.
- Some of them are only valid for flat surfaces.
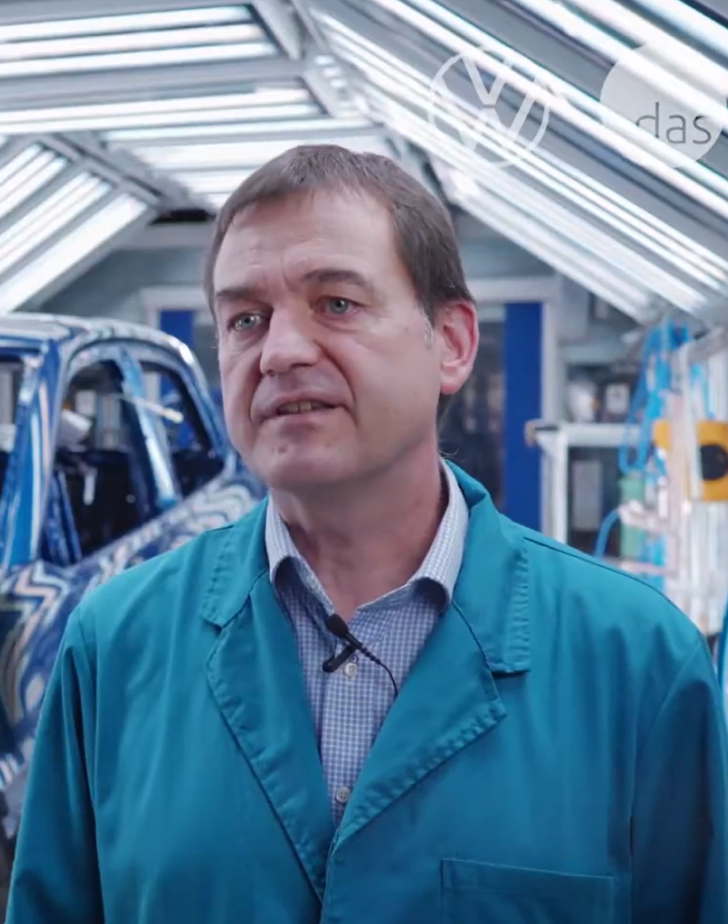
Frank Uhlemann, the responsible for the Painting process Planning at VW Navarra, points out the needs for new quality control methods in the automotive industry.
Why das-Nano Irys?
Coating thickness measurement Technology that allows to:
- Save costs: time, materials & energy
- Reduce reworks & wastes
- Improve quality control
- Learn fast from real-time data and Analytics
- Minimize environmental impact
The das-Nano solution A patented Terahertz Waves technology
das-Nano has solved the challenge thanks to the Irys system, a patented non-contact system that, using terahertz waves and proprietary algorithms developed by das-Nano, measures the thickness of each coating layer of a car body in a non-destructive way.
The main advantage of this system is the ability to provide the vehicle manufacturer with information, hitherto unavailable, of its painting process, and propose a 15% saving in the cost of the process thanks to the reduction of materials, energy and defective pieces, with the corresponding environmental impact reduction.
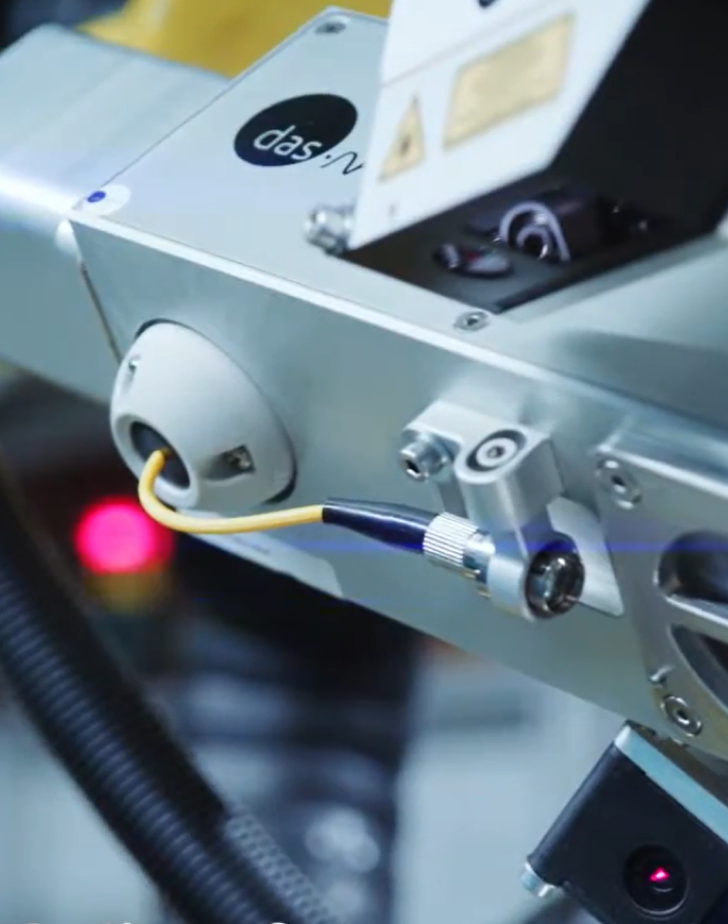
The system allows fast and non-contact inspection of materials. Real-time thickness measurements of each applied paint and clear coat layer (wet, dry and cured), are obtained, providing the customer with a more reliable painting process and early detection of defective pieces. In addition, the system is fully automated and features a self-calibration system that requires no calibration stops.
Applicable to any type of substrate: metallic, polymeric, composite, etc. and also on flat and curved surfaces, has an excellent accuracy of 1 micron.
“It offers high spatial resolution below the millimeter, down to the micron unit, can pass through most materials that have low electrical conductivity, and are low-energy waves, harmless to humans,” explains Eduardo Azanza, co-founder and CEO of das-Nano.
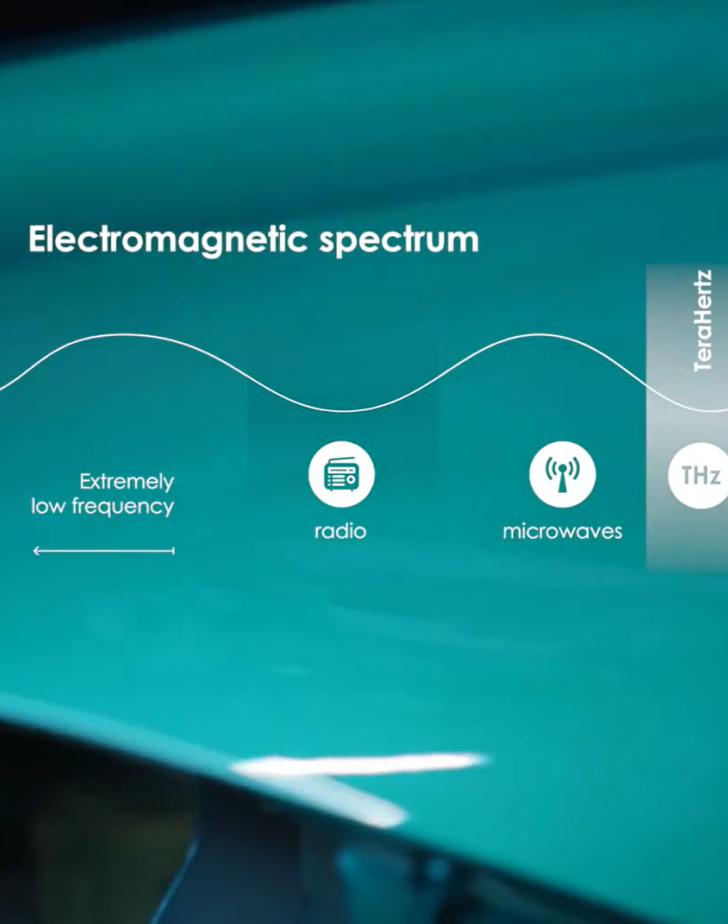
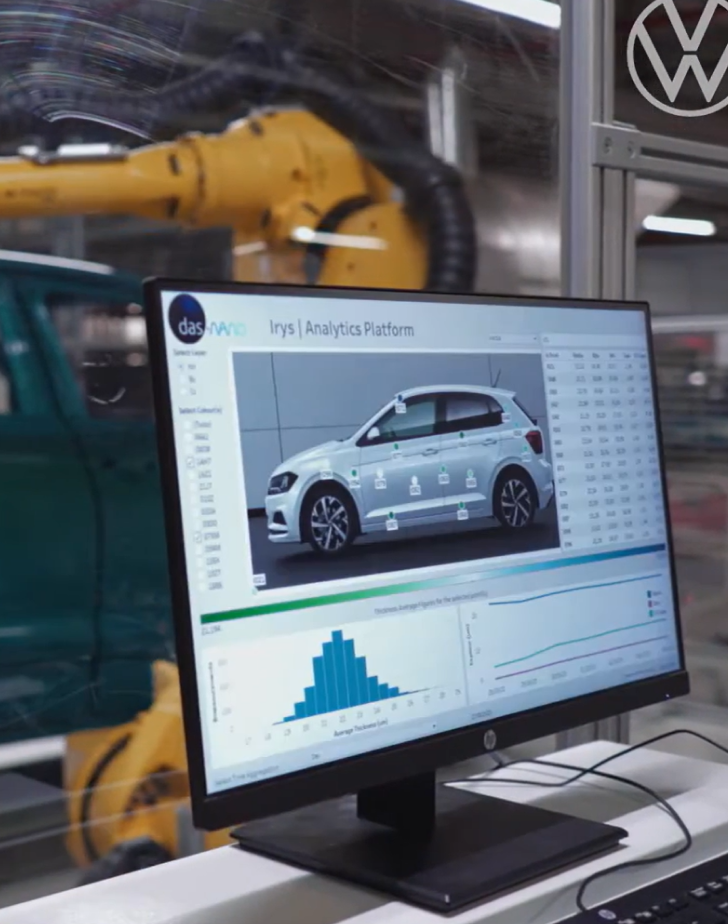
Volkswagen and das-Nano
Discover the Volkswagen and das-Nano
coating thickness measurement success story.
Want to dive deeper into how Volkswagen is optimizing quality control with das-Nano’s cutting-edge technology? Download the full success story and explore the impact of advanced coating thickness measurement in action.
The Irys system is complemented with the das-Nano Analytics platform that achieves:
- Real-time data on the thickness of paint applied in each layer
- Control and monitoring of the painting process
Early detection of quality errors and correction - Complete knowledge for a more robust process
das-Nano’s THz technology has been chosen after an international tender by the world’s leading car manufacturer, Volkswagen, for the world’s first installation of the paint thickness inspection system at Volkswagen Navarra’s facilities. Irys is successfully in full operation since July 2020, 24/7.
The automotive industry will continue to rely on these new inspection technologies for the painting processes, not only for the direct benefits of their application but also for the significant environmental impact reduction. Thanks to one single Irys system, 50 kWh/car can be reduced in the painting process, which implies more than 16 GWh/year in a main car manufacturing plant such as VW Navarra: a reduction in CO2 emissions higher than 7,000 CO2 ton/year!